The process from A to Z
IVD product development is a delicate and complex procedure. Only by using the purest of products, highly skilled professionals and effective communication do we reach the optimal product development process. Since we take pride in our in-house processes, we are more than pleased to present to you a closer look behind the doors of our facility on the comprehensive overview of product development at Future Diagnostics: the process from A to Z.
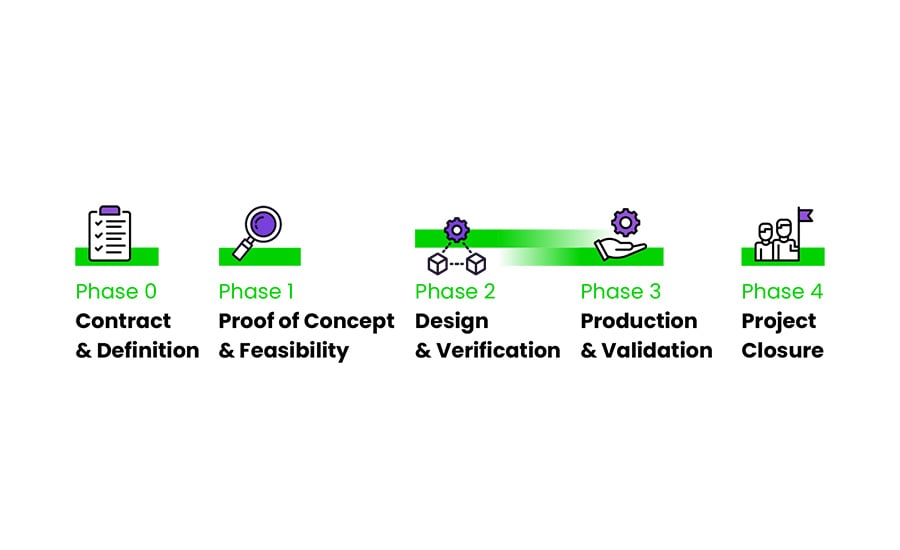
Our step-by-step action plan
Every single one of our customers will agree: by working with our proven step-by-step action plan we control every single part of the product development process. There are 4 stages to reach the set goals:
– Contract and Definition
– Proof of Concept and Feasibility
– Design and verification
– Production and validation
These steps act as the pillars that guide us and keep us focused to adequately and efficiently run our processes without losing precious time and focus.
A project is always supervised by two of our experts. The expert responsible for the technical part of the IVD product development process is constantly observing and controlling the terms of the agreement. Our second expert controls the set time frame and overviews the costs. During the development process we regularly report the progress of the project to our client. Also, our SharePoint environment enables our clients to have a real-time view of the progress. It is vital to have transparent communication between us and our client to keep the development process efficient thereby saving time and costs.
Phase 0; contract and definition
When developing an IVD test the first thing to do is set up a non-disclosure agreement between both parties, and subsequently a signed contract covering the work that has been agreed upon: Phase 0. We determine the request based on the input from our technical experts. The contract consists of a high-level plan, timeline, an indication of the cost and of the project, the scope of the technical work, key parameters, deliverables, and timelines and budget for phase 1. As soon as all parties support the contents of the contract the Proof-of-Concept and Feasibility phase follows.
Phase 1; proof of concept and feasibility
Phase 1 is about establishing proof of concept and feasibility of the project. During Proof-of-concept, we aim to establish that the concept products has practical potential. The questions we ask ourselves, often during a proof-of-concept study, are: ‘What critical raw materials are needed and which ones are of the best quality?’ Similarly, ‘Which novel technologies guarantee maximum results?’ In the feasibility study the scope shifts towards establishing key critical materials, required assay components and protocol, in order to pass with an acceptable degree of certainty the mutually agreed key assay specifications within the set time frame and analyze the predetermined budget. The completion of this phase gives us the opportunity to present to our client an overview of the main raw materials and the techniques we will be using. By providing a realistic estimate of the costs to proceed with the IVD product development process, we also present an insightful transparent plan in which we incorporate an overview of possible risks that will be mitigated during the subsequent development phases.
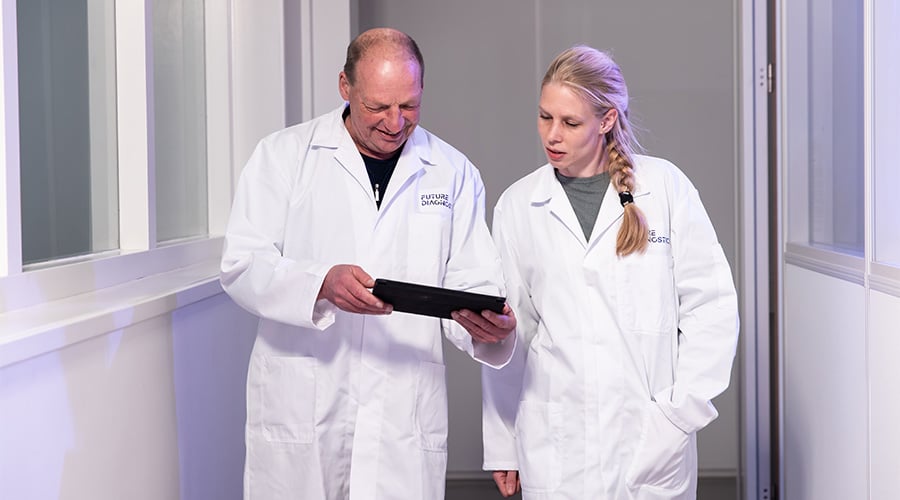
Phase 2; design and verification
Once both parties agree and give the ‘go-ahead’ for the next phase in the IVD product development, we start to continuously optimize the product design to ensure that the IVD test improves to meet all requirements of the pre-determined product development plan. This is our promise to you. Our team of experts is committed to establishing critical test parameters before finalizing the test design.
Upon finalizing the test design the product design is then verified by testing assay parameters according to the design demands at our R&D facility. Stability studies provide indicative shelf-life data.
Phase 3; IVD production and validation
In this phase of the IVD product development process, the product is handed over to an ISO13485 certified and/or FDA registered production facility. At Future Diagnostics, this facility is present in-house. However, our client is always in control to decide on a production location of their own choosing. No matter how much we stand behind our own methods, it’s always the client’s decision.
In the determined production location the test is put into production and preparations are made for technical and clinical validation. Once the end product is available we conduct validation studies and (accelerated) stability tests. Technical validation is conducted at our facilities according to the latest CLSI guidelines. During this validation process everything is meticulously documented into reports, compliant to ISO 13485. We document every step in the process, ensuring that each stage is back-traceable. In Europe analytical performance is part of the validation phase.
Phase 4; Completion
Once we are able to deliver a high-quality product, it is now time to complete the process. We hand over all technical documents and applicable parts of the design history file to our client. This document is in accordance with the regulations for medical devices in the country of your choice. All expenses are already included in the development costs. The end product is now in full legal ownership of the client and only the client’s name is mentioned.
IVD product development is an extensive process and can hardly be captured in one blog only. That’s the reason we give you an overview of IVD product development by Future Diagnostics. If you are interested in more information on our daily activities or perhaps looking for collaboration in the field of IVD product development, please contact us. We are passionate about our profession and would love to share our expertise with you.
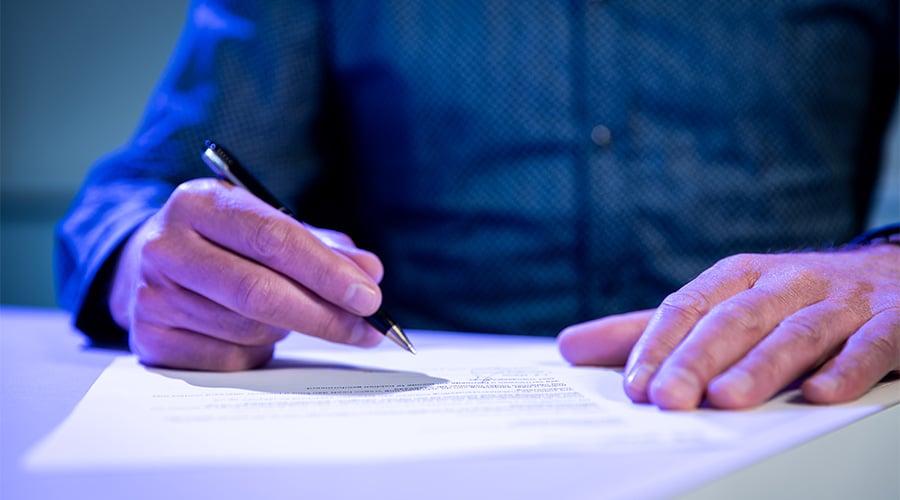
References
Many leading biotech and in vitro diagnostic (IVD) medical devices companies appreciate our proven, transparent approach to assay development.
Let's work together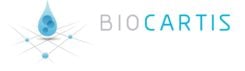
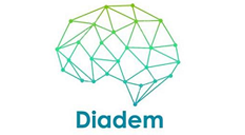
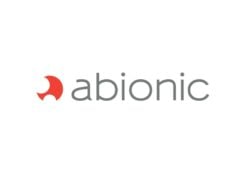
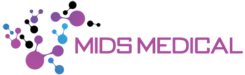
IVD test and product development
Our enthusiastic and skilled experts will help your R&D team accelerate and bring your immunoassay to market rapidly